

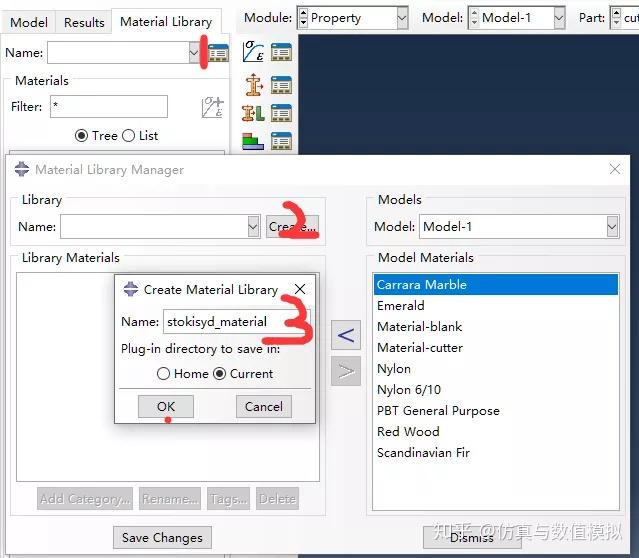
These methods fall generally into two categories, i.e., analytical and numerical methods.
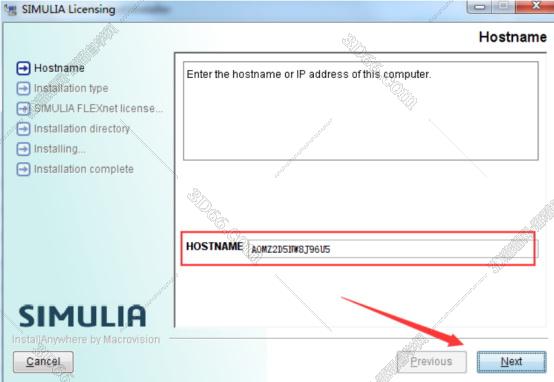
To overcome the aforementioned drawbacks associated with experimental tests, various micromechanical approaches have been proposed to establish a closed-form relationship between elastic properties at the lamina scale and the elastic properties at the constituent scale. This procedure may, for instance, costs millions of dollars and lasts for years to generate the experimental data of mechanical properties for the design of aircraft structures. However, it must be repeated whenever the constituents (fibre and matrix) and/or microstructure characteristics (fibre volume fraction) are altered. Experimental tests are ideal solutions to evaluate the mechanical properties of a composite lamina. Applications of FRP composite laminates to create engineering structure models fundamentally require mechanical properties as inputs. Fibre-reinforced polymer (FRP) composite laminates have been widely used in aerospace, automotive, and wind energy industry due to their excellent material properties such as high stiffness-to-mass ratio, high strength, and light weight.
